Advancements in Aseptic Fill-Finish Technologies
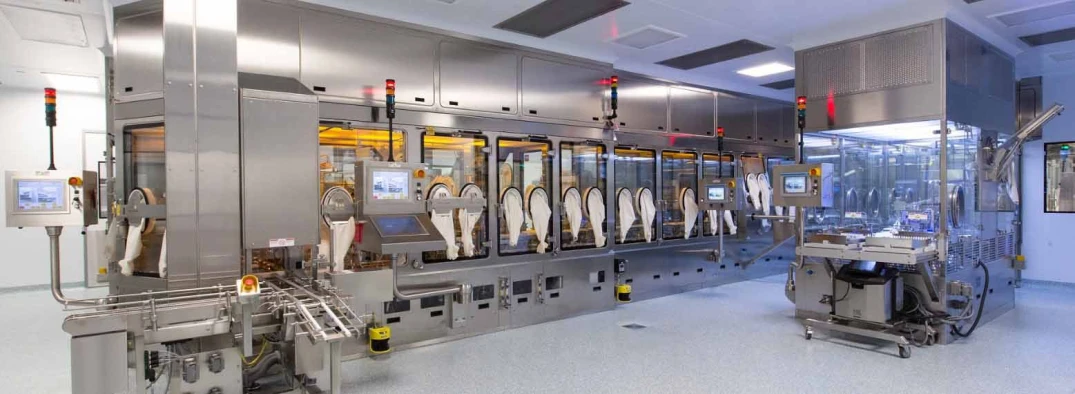
In the world of bioprocessing, maintaining the utmost sterility and integrity of products is of paramount importance. Aseptic fill-finish processes play a critical role in the production of biopharmaceuticals, vaccines, and other life-saving drugs. These processes involve the filling and sealing of sterile drug products in containers without compromising their purity.
Over the years, advancements in aseptic fill-finish technologies have revolutionized the bioprocessing industry, offering increased efficiency, reduced contamination risks, and enhanced product quality.
In this article, we will explore some of the key advancements in aseptic fill-finish technologies that are shaping the future of pharmaceutical manufacturing.
Advanced Barrier Technologies
The development of advanced barrier technologies has been instrumental in improving the sterility of aseptic fill-finish processes. Barrier isolators and restricted access barrier systems (RABS) have become standard features in modern pharmaceutical manufacturing facilities. These systems create physical barriers between operators and the filling process, minimizing the risk of microbial contamination.
In addition to physical barriers, advancements in barrier technology also include the use of innovative materials that provide an extra layer of protection. High-performance plastics, such as fluoropolymers and silicones, are now commonly used for gaskets, seals, and tubing to ensure a reliable and secure aseptic seal.
Single-Use Systems
One of the most significant advancements in aseptic fill-finish technologies is the widespread adoption of single-use systems (SUS). Traditional stainless-steel equipment requires extensive cleaning and validation processes, which can be time-consuming and expensive. Single-use systems, on the other hand, eliminate the need for cleaning and sterilization between batches, reducing the risk of cross-contamination and speeding up production processes.
Companies like Venair have played a pivotal role in providing high-quality single-use systems custom fitted for every isolator and filling needle model, using in-house molded pass-throughs in the beta bags to ensure the integrity of bioprocessing operations. These components are designed to be disposable after use, reducing the risk of product carryover and making it easier to maintain aseptic conditions throughout the production cycle.
Robotics and Automation
Automation has transformed many aspects of pharmaceutical manufacturing, and aseptic fill-finish processes are no exception. Robotic systems are now being employed to perform critical tasks like container loading, filling, capping, and inspection. These robots are highly precise and can operate in a sterile environment without introducing contamination risks associated with human intervention.
By implementing robotics and automation, pharmaceutical companies can improve the consistency and speed of their fill-finish operations, resulting in higher production yields and reduced labor costs. Furthermore, these systems can operate 24/7, contributing to a more efficient and productive manufacturing process.
Real-time Monitoring and Process Control
Advancements in sensor technology and data analytics have enabled real-time monitoring and process control in aseptic fill-finish operations. Continuous monitoring of critical process parameters, such as temperature, pressure, and airflow, allows for immediate detection of deviations and rapid corrective actions.
Furthermore, the integration of advanced analytics and machine learning algorithms can help predict and prevent issues before they occur, optimizing the manufacturing process and minimizing the risk of product defects. This level of control and monitoring ensures that products meet the highest quality standards while reducing the likelihood of batch failures.
Regulatory Compliance and Validation
As the pharmaceutical industry continues to evolve, regulatory agencies are also updating their guidelines and requirements for aseptic fill-finish processes. Advancements in technology have allowed for more efficient validation processes, ensuring compliance with regulatory standards.
Companies like Venair are at the forefront of providing products and solutions that meet the rigorous requirements of regulatory agencies, helping pharmaceutical manufacturers navigate the complex landscape of compliance.
Advancements in aseptic fill-finish technologies have ushered in a new era of efficiency, sterility, and product quality in the bioprocessing industry. The integration of single-use systems and advanced barrier technologies has transformed the way pharmaceuticals are manufactured.
Conclusions
As the industry continues to evolve, companies like Venair will play a crucial role in providing innovative solutions that meet the ever-increasing demands for aseptic fill-finish processes. These advancements not only benefit pharmaceutical manufacturers but also ensure the safety and efficacy of life-saving drugs for patients around the world.