Revolution in Biopharmaceuticals: Continuous Manufacturing
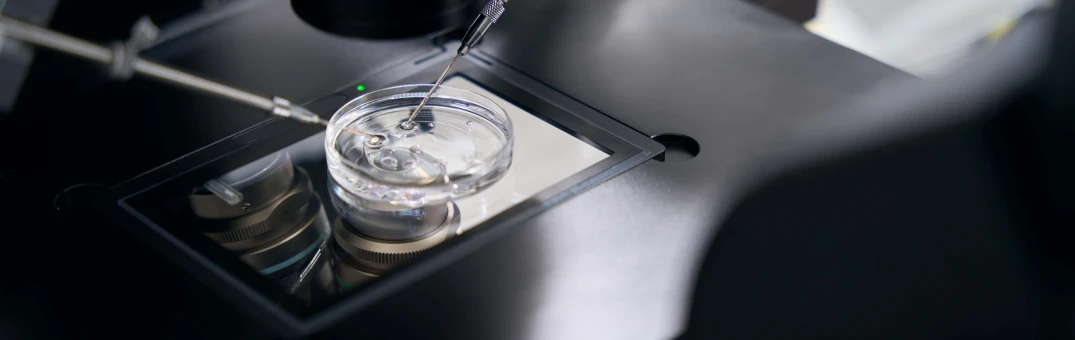
The biopharmaceutical industry has been witnessing a significant transformation in recent years, with the adoption of continuous manufacturing techniques taking center stage. Traditional batch manufacturing processes have long been the industry standard, but continuous manufacturing is emerging as a game-changer that promises improved efficiency, cost-effectiveness, without compromising the quality of the final product
In this blog article, we will explore the concept of continuous manufacturing in biopharmaceuticals and its impact on the industry.
What is continuous manufacturing in biotech?
Continuous manufacturing is a production method that differs from traditional batch processes in several key ways. Instead of manufacturing biopharmaceuticals in discrete, separate batches, continuous manufacturing involves a continuous, uninterrupted process. This means that raw materials are constantly fed into the production line, and the final product is continuously collected at the other end.
Advantages of Continuous Manufacturing:
-
Enhanced Efficiency: One of the primary advantages of continuous manufacturing is its ability to streamline the production process. With no need to start and stop for each batch, there is a significant reduction in downtime, resulting in higher overall productivity.
-
Quality: Another primary advantage of continuous bioprocessing is that it can also positively affect the quality of the final product. Besides requiring tighter control and monitoring, the state of the cells is usually analyzed more in-depth than in batch and fed-batch processes and the stable conditions are less stressful for the cells.
-
Cost Savings: While the initial setup for continuous manufacturing may be more expensive than traditional batch processes, the long-term cost savings are substantial. Reduced labor, less waste, and optimized resource utilization contribute to lower production costs. It also usually allows for smaller equipment and a reduction of the facility footprint.
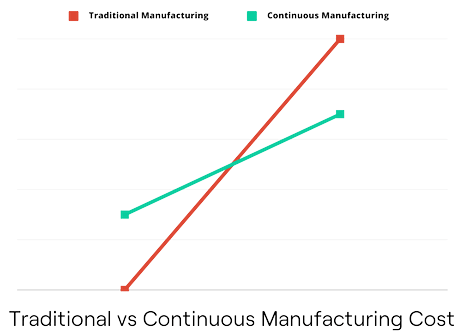
-
Faster Time to Market: Continuous manufacturing accelerates the production timeline. This allows biopharmaceutical companies to bring their products to market more quickly, responding faster to changing market demands and patient needs.
-
Flexibility: Continuous manufacturing is adaptable to various scales, making it suitable for both small-scale research and large-scale production. This flexibility is especially advantageous in the rapidly evolving biopharmaceutical landscape.
Applications in the biopharmaceutical industry
Continuous manufacturing has found widespread applications in the biopharmaceutical industry. Some of the key areas where it is making an impact include:
-
Monoclonal Antibodies: Continuous manufacturing is particularly well-suited for the production of monoclonal antibodies, a cornerstone of biopharmaceuticals. The continuous process ensures consistent antibody yields and quality.
-
Vaccines: Vaccine production can benefit from continuous manufacturing, as it allows for more rapid response to emerging infectious diseases and the production of large quantities in a shorter time frame.
-
Cell and Gene Therapies: The production of cell and gene therapies often requires strict control over culture conditions. Continuous manufacturing can provide this level of control, ensuring the viability and effectiveness of these advanced therapies.
Challenges of continuous manufacturing
While continuous manufacturing offers numerous advantages, it also presents challenges and considerations:
-
Regulatory Approval: Regulatory agencies such as the FDA have been following the advances of continuos manufacturing during the last years with great interest and very positive impressions. Recently, the FDA has published its final contiuos manufacturing guidance: ICH guideline Q13 on continuous manufacturing of drug substances and drug products - Scientific guidelines.
-
Process Complexity: Continuous manufacturing processes can be more complex to design and operate than traditional batch processes, requiring specialized expertise. This is specially true for the downstream, traditionally considered the bottleneck for widespread continuous production implantation. However new continuous purification tools and methodologies that will aid in this regard are being developed and implemented in the later years.
-
Equipment Investment: Transitioning to continuous manufacturing may require significant capital investment in new equipment and technology.
Conclusions
Continuous manufacturing is poised to revolutionize the biopharmaceutical industry by offering increased efficiency, improved quality control, cost savings, and faster time to market.
As the industry continues to embrace this innovative approach, companies like Venair are at the forefront, providing the necessary components, such as silicone tubing and polyethylene 2D bags, to support the integration of single-use systems for continuous bioprocessing. With these advancements, biopharmaceutical companies can look forward to a future of enhanced productivity and the development of life-saving therapies with greater ease and speed.