The Role of TPE Tubing in Biotechnology: A Look at Venair's VenaBio® Flex
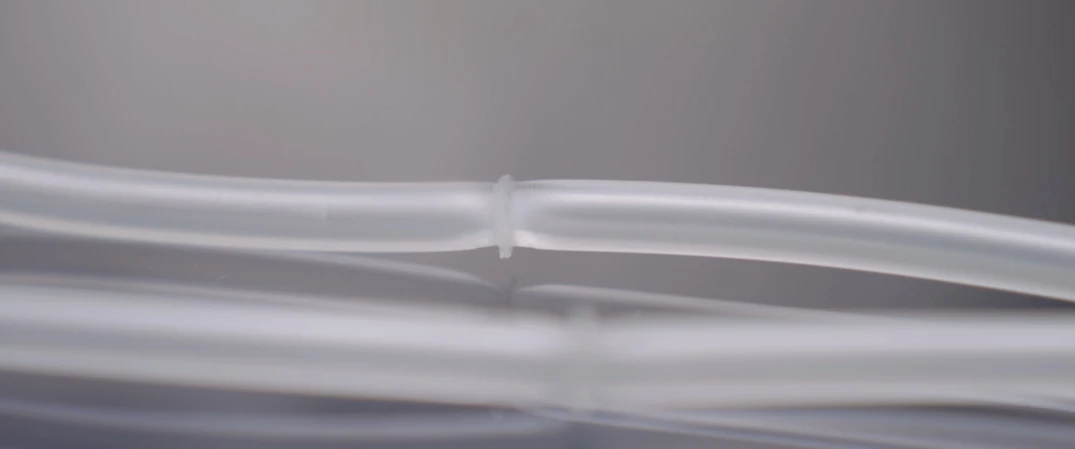
Thermoplastic elastomer (TPE) tubing has become an essential component in the biotechnology and biopharmaceutical sectors, renowned for its unique blend of flexibility, durability, and safety. Unlike traditional materials, TPE tubing is designed to meet stringent industry requirements, providing a reliable solution for transporting delicate substances such as vaccines, biologics, and cell cultures.
Venair, a prominent manufacturer specializing in flexible tubing solutions for biotech applications, offers a standout option with VenaBio® Flex, a thermoplastic tubing product specifically engineered for use in sensitive biopharma processes. In this article, we’ll explore the general advantages of TPE tubing and then examine the specific features that make VenaBio® Flex a trusted choice for today’s biotechnology applications.
Understanding TPE Tubing and Its Advantages for Biotechnology
Thermoplastic elastomers are a versatile class of polymers that combine the flexibility and elasticity of rubber with the ease of processing and recyclability of plastics. For biotechnology applications, thermoplastic tubing offers several advantages over conventional materials such as silicone and PVC. Here are some of the key characteristics that make TPE flexible tubing so valuable in this sector:
- Biocompatibility: TPE tubing is highly compatible with sensitive biopharmaceutical products. Free from additives like plasticizers, TPE ensures that transported fluids remain uncontaminated, which is crucial in applications like vaccine and medication production.
- Sterilization Compatibility: TPE can withstand rigorous sterilization methods, including autoclaving (depending on autoclave conditions) and gamma irradiation, without compromising its structural integrity. This compatibility makes TPE ideal for applications requiring high levels of sterility, such as bioreactors and single-use bioprocessing systems.
- Flexibility and Resilience: thermoplastic tubing maintains its flexibility across a broad range of temperatures, allowing it to function in various environmental conditions without becoming brittle. This flexibility reduces kinking and ensures consistent flow, making it easier to incorporate into complex biotech setups.
- Eco-Friendliness: As a thermoplastic, TPE can be recycled, reducing waste in applications that benefit from single-use systems. This property aligns with sustainability goals, which are increasingly important to biotechnology and biopharma companies worldwide.
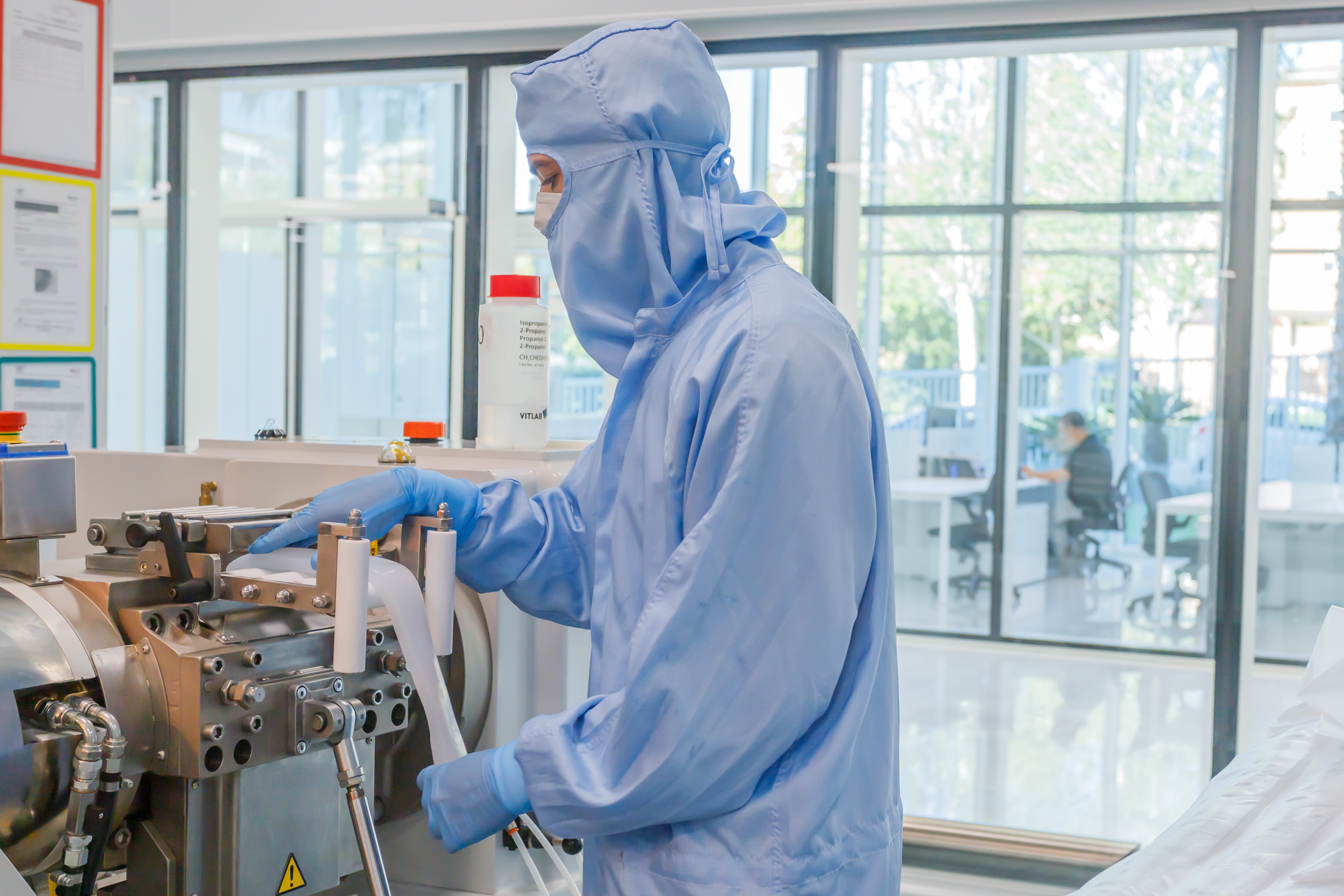
- Chemical Resistance: The chemical stability of TPE allows it to resist degradation when exposed to cleaning agents or specific biopharma formulations, ensuring tubing longevity and cost efficiency.
These properties make TPE tubing an excellent option for transporting sensitive substances in biotechnology, ensuring purity, flexibility, and durability.
Venair’s VenaBio® Flex: TPE Tubing Designed for Biotech Applications
As a leading provider of tubing and kit solutions for the biotechnology and pharmaceutical industries, Venair has harnessed the advantages of TPE in its VenaBio® Flex tubing. VenaBio® Flex stands out for its tailored design, meeting the specific needs of biotechnological applications while maintaining compliance with regulatory standards and ensuring safe transport.
Key Features of VenaBio® Flex
- Compliance with Industry Standards: VenaBio® Flex complies with international regulatory requirements, including USP Class VI, ISO 10993-5, and FDA 21 CFR 177.1810 standards. This compliance makes it a secure choice for biotech companies that require reliable, approved materials to protect product integrity.
- Single-Use Ready: In the biopharma industry, single-use systems are essential for preventing cross-contamination and increasing process efficiency. VenaBio® Flex is ideal for these applications, simplifying workflows, minimizing cleaning requirements, and reducing downtime.
- Flexibility Under Diverse Conditions: VenaBio® Flex retains flexibility enabling smooth handling and installation in complex tubing setups. This characteristic helps maintain a steady, controlled flow, essential for applications involving the precise transfer of materials.
- Chemical Compatibility: In biotech processes, tubing must withstand exposure to various solutions without compromising material integrity. VenaBio® Flex's chemical resistance allows it to perform effectively with diverse formulations and cleaning agents, ensuring longevity and consistency in performance.
- Exceptional Performance in Peristaltic Pump Applications: One of the defining features of VenaBio® Flex tubing is its outstanding durability in peristaltic pump applications, a critical requirement in many biotechnology processes. Peristaltic pumps are widely used for their ability to handle sensitive fluids without contamination, but they place significant wear on tubing.
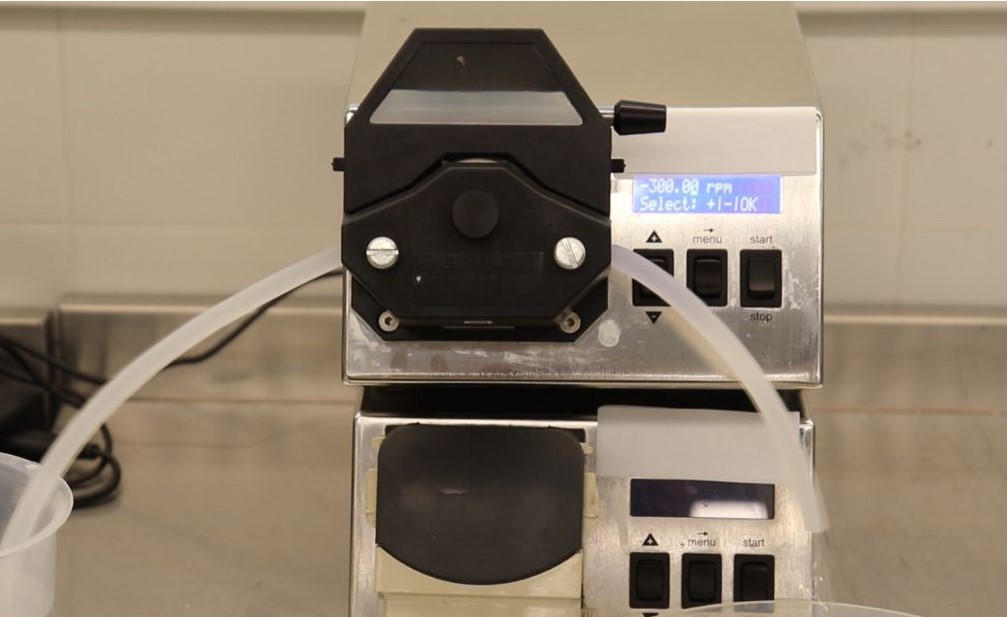
This robust performance highlights VenaBio® Flex's resilience and longevity under continuous use, even after sterilization procedures commonly required in biopharmaceutical production.
Applications of VenaBio® Flex in Biopharmaceutical Processes
The adaptability of VenaBio® Flex makes it suitable for various biotech applications, from cell culture production to downstream bioprocessing. Its integration into Venair’s Biotech division portfolio also allows for tailored solutions, where VenaBio® Flex tubing is combined with specialized connectors and assemblies for specific needs. This customization supports the critical requirements of biotech firms, ensuring that sensitive products are managed with the highest levels of safety, precision, and compliance.
Thermoplastic Tubing as a Standard in Biotech Innovation
The benefits of TPE tubing, from its biocompatibility to its flexibility and sterilization readiness, make it an invaluable material in the biotechnology field. VenaBio® Flex builds upon these TPE properties to create a solution specifically crafted for the demanding applications within biopharmaceutical processes.
By choosing VenaBio® Flex, biotech firms can streamline their processes, minimize contamination risks, and maintain product purity—factors crucial for advancing the development and delivery of critical therapies.