Flexible manifolds for Electric Thermal Management Systems
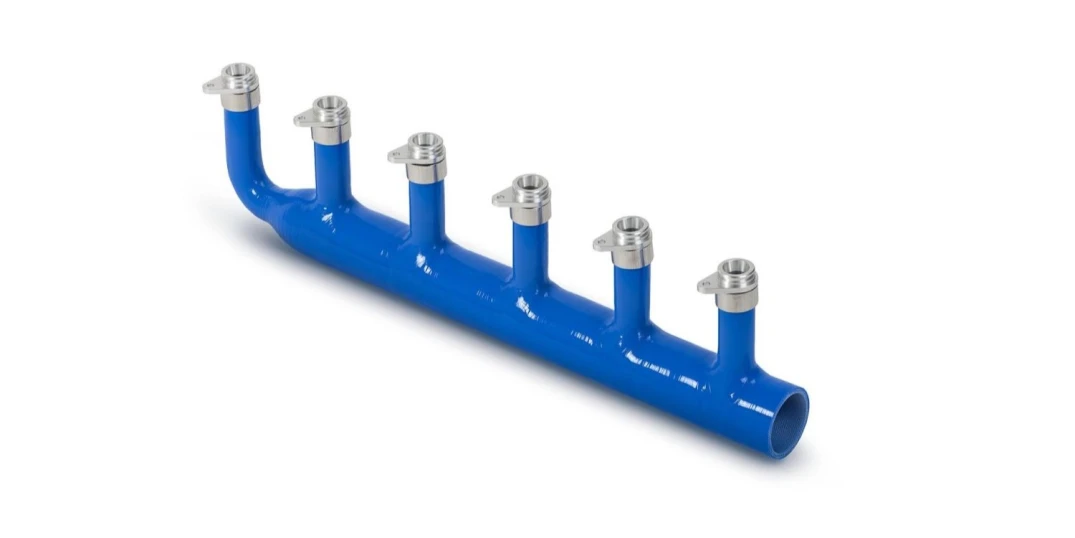
Optimizing Cooling Systems for Electrical Systems: Compact Spaces, Custom silicone hoses
In the realm of electrical systems, the challenge of efficiently cooling components within tight spaces is paramount. This necessity has given rise to innovative solutions in the form of custom-designed cooling systems, particularly those employing silicone or other elastomers.
Minimizing Refrigerant Leakage in Silicone Hoses
Minimizing the risk of refrigerant leaks is crucial. Even a minor leak can lead to catastrophic consequences such as short circuits and system failures. Custom-shaped components, manufactured as single pieces, significantly reduce the risk of leaks, ensuring the integrity of the cooling system.
Basically, the objective is to reduce the risk points of leakage to a minimum. It is very common that in initial prototypes an attempt is made to create a shape from many standard parts (straight sections, elbows and reductions) connected with couplers, T-shapes or double nipples. At the level of concept and design, they are much simpler. But once the system advances to a more mature state, it is preferable to reduce to a minimum the connection points where there is a possible risk of leakage. This also substantially reduces the complexity of the system in terms of the number and type of components. Since it is possible to go from a network of many different standard tubes and connections to a single, unique and consistent shaped part.
These systems with many connected components are called "Frankenstein Systems", while the optimal solutions with a single part are the so-called "shaped parts" or manifolds (in case they have a side outlet).
Maintaining Consistent Conductivity
Preserving the conductivity of the cooling medium is equally vital. Venair achieves this by employing materials that minimize contaminants and their impact on conductivity. This meticulous approach ensures that the cooling system operates at optimal efficiency without compromising the properties of the conveyed fluid.
Addressing Constricted Spaces
Electrical systems often operate within confined spaces, necessitating cooling solutions tailored to fit within these constraints. Venair, a leading company in this field, specializes in engineering, designing, and producing components with various lateral outlets, allowing for seamless integration into the client's cooling designs.
Venair: Pioneering Complex Cooling Systems
Venair specializes in the design and production of tubes and manifolds in various configurations to meet the demands of specialized applications. These include Battery Thermal Management Systems for Battery Electric Vehicles (BEVs), Thermal Management Systems for Fuel Cell Electric Vehicles, and cooling solutions for high-complexity electronic systems such as Data Centers.
Addressing Fire Safety Concerns
Given the critical nature of electrical systems, fire safety is a top priority. Venair engineers solutions using materials and constructions that meet the highest flammability certifications, such as UL-94 Flammability compliance, ensuring the utmost safety standards are upheld.
Embracing Future Trends
The future of industry lies in electrification, advanced electronic systems, and customized geometries to fit increasingly compact spaces. Venair's specialization in sophisticated cooling systems aligns with these trends, emphasizing durability, high quality, and adaptability to meet the evolving needs of the market.
In conclusion, Venair stands at the forefront of developing cutting-edge cooling solutions for electrical systems, catering to the demands of modern industry while prioritizing safety, efficiency, and innovation.