How to select the correct hose for Organic Acid Technology?
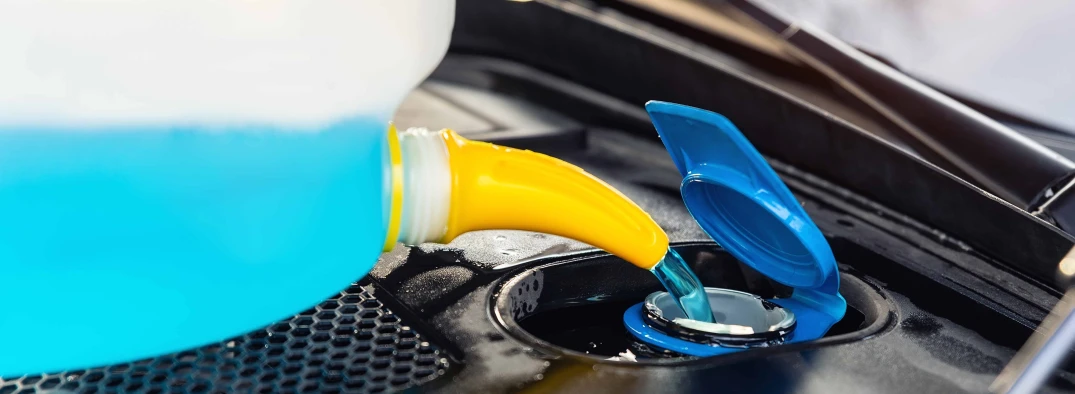
Organic Acid (additive) Technology (OAT) are long life/extended coolants base on minimally depleting carboxylate technology. This technology provides excellent protection from corrosion and a long working life.
Another typical coolant is Hybrid organic acid technology (HOAT) that has silicate inhibitors for improved aluminum protection.
It is important to choose the correct hose depending on the coolant and working conditions to prevent swelling by possible penetration of the media into the material and between layers and damage the fabric reinforcement and subsequent leading to hose failure.
Silicone, the perfect material?
Silicone is one of the most stable rubbers thanks to its flexibility and aging resistance after long-time exposure to extreme conditions, such as temperature, ozone, and weather. It can resist environments in which other rubbers might suffer much more degradation and therefore, withstand more service life with coolants.
Venair Capabilities
Since there are a lot of different coolants in the market depending on the needs and requirements, Venair has gain expertise in testing chemical compatibility on different rubbers to be sure that our materials are specifically compatible with the coolant proposed by our customers.
The different tests at Venair:
Block oven: evaluation of chemical compatibility of silicone and other rubbers by immersion in coolant at certain temperature and time. This test is according to ISO 1817 (Determination of the effect of liquids). Damage and degradation measured by volume, hardness, tensile strength, and elongation changes.
Pulsator: Mechanical fatigue evaluation by combining pressure, chemical and temperature degradation in hose prototypes. Perfect to replicate real conditions.
Chemical testing machine: chemical transfer circuit for hose fatigue. Capability to test the chemical compatibility of our hoses at different concentrations, pressure, flow, and temperatures, and evaluate the degradation under different conditions.
Hydrostatic testing machine: to evaluate the hydrostatic pressure resistance of hoses. Also, the variations on the working pressure and bursting pressure due to degradation. Complementary machine to quantify the degradation after fatigue in other machinery.
Conclusions
All this machinery mentioned and capacity, together with the material testing capabilities, allows Venair to offer products based on key features such as security, durability, design efficiency, sustainability, innovation, damage prevention and operational security optimization.
Also, this equipment leads us to adapt our hoses to certain normative compliance thanks to the test capability that in many cases allows us to replicate the official tests needed for certain applications / sectors prior to official certification.