Cleanliness tests (ISO 16232)
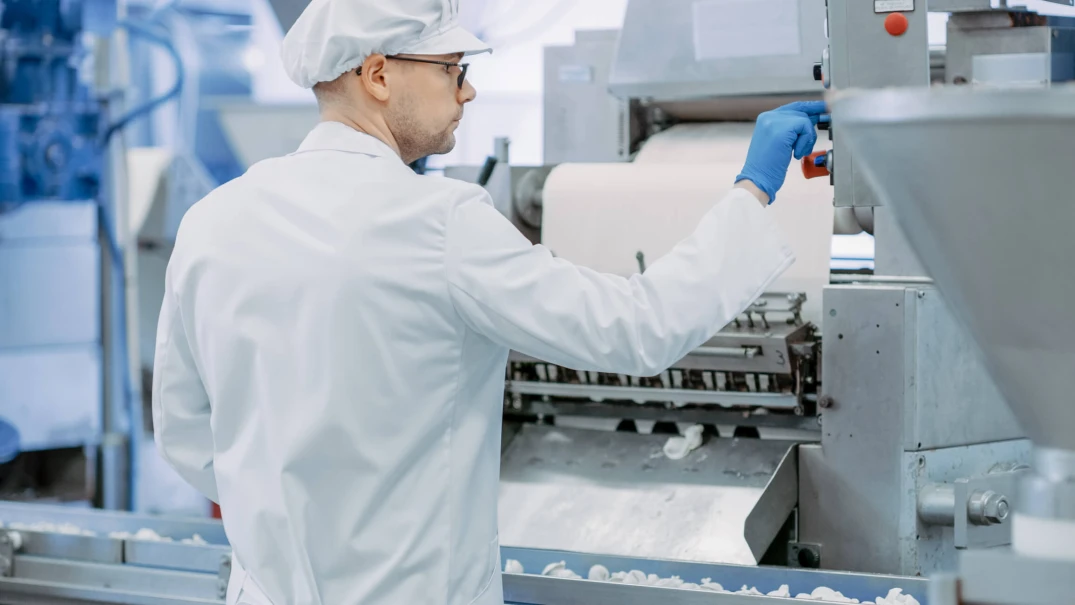
At Venair, we understand the importance of adhering to comprehensive cleaning standards for our hoses. Even the smallest speck of dirt can cause significant damage to components and systems, potentially leading to blockages. That's why our quality engineers provide documentation and conduct regular tests to meet the most stringent guidelines and customer requirements regarding cleanliness.
ISO 16232 Cleaning Controls
Venair recommends consistently using ISO 16232 as it's the latest international standard for component contamination. This standard specifies rigorous requirements for applying and documenting methods for determining particle contamination in functionally relevant components and systems (cleanliness inspection) of road vehicles.
The aim of the standard is to enhance informational quality and comparability of test results. It also standardizes the expression of cleanliness specifications and test results within the automotive industry's quality chain.
The cleanliness inspection we conduct in accordance with the standard forms the basis for technical cleanliness assessment, carried out in scenarios such as:
Initial inspection and evaluation
Inspection of incoming and outgoing components
Quality control or supervision of cleaning-related manufacturing processes
Evaluation and inspection of incoming and outgoing components
Essentially, the cleanliness tests we perform on hoses involve extracting 90% or more of the residual contamination from the hose's interior and transferring it to a filter patch for analysis.
During the analysis, we may conduct the following tests:
- Gravimetric (mass contamination)
- Maximum particle size
- Particle count and distribution
- Particle identification
- Gravimetric
Gravimetric analysis
Is a technique for determining the quantity of an analyte (the analyzed ion) by measuring mass. The principle behind gravimetric analysis is that the mass of an ion in a pure compound can be determined and then used to find the percentage of mass of the same ion in a known quantity of an impure compound.
Maximum Particle Size
Particle size is a notion introduced to compare the dimensions of solid particles (specks), liquid particles (droplets), or gas particles (bubbles). The maximum particle size is the maximum acceptable particle dimension as per the standard.
Particle Count/Distribution of Particle Size
Particle counting can be done online to monitor contamination levels in air environments such as clean rooms or in cleaning solutions used for precision cleaning. Particle Size Distribution (PSD) is the relationship between particle size and concentration, a key parameter defining the interaction of light with natural waters and thus crucial for natural water optics.
Particle Identification
Particle identification is the process of using information left by a particle passing through a particle detector to identify the particle type. It's essential for studying interactions in particle physics. Special detectors can be constructed to identify electrons and muons as they have unique signatures when passing through matter.
Quality Control
Cumulative tests have been conducted to understand the behavior of the finished product under steam circulation without other agents, simulating SIP processes as used in food and pharmaceutical industries. Venair has refined testing equipment for these tests, optimized over time to conduct faster tests.
Procedure:
- Conduct a water pressure test at 10 bar for 30 minutes.
- Cycle with internal steam circulation*.
- After a cycle, cool the hose with water circulation and allow 30 minutes of rest (hose stabilization).
- Visual inspection of the hose.
- Purge and new cycle.
- After every 20 hours, conduct a retention test to ensure hose functionality.
- Conduct cycles until hose failure.
Additionally, we simulate CIP (hot water) with Venair hoses to understand the behavior of hot water circulation without other agents.
Procedure:
- Conduct a water pressure test at 3 bar for 30 minutes.
- Cycle for 2 hours with internal water circulation at 2 bar and 85°C.
- After the cycle, remove the hose from the test bench and cool to room temperature for 1 hour (hose stabilization).
- Visual inspection of the hose.
- New cycle.
- After every 10 hours, conduct maintenance testing to ensure hose functionality.
- Conduct cycles until hose failure.
Through these tests, we ensure compliance, offer maximum quality, and guarantee the best advice and application procedures to maximize hose lifespan. The cleaning documents we provide offer information on hose quality and recommendations. However, they do not define any cleanliness limit values for specific components or systems. The degree of cleanliness required for a specific component or system depends on several highly individual factors.
Cleaning specifications should be determined only by specialists who not only understand the component in question but also the system it integrates into, subsequent usage conditions, technically viable practices, and potential consequences for manufacturing processes and the supply chain.
At Venair, we conduct various tests.
From a technical standpoint, ISO 18413 (Hydraulic fluid power — Component cleanliness — Inspection document and principles related to contaminant extraction and analysis, and data reporting) is the correct approach for determining particles in a hydraulic component, widely used in the sector.
Additionally, ISO 4405, related to hydraulic fluid contamination rather than components, is another cleanliness standard we comply with and regularly test against.